The shape and size of industrial aluminum profiles can be customized according to specific needs.
First, the basic characteristics and advantages of aluminum profiles
Aluminum profiles are materials with various cross-section shapes made of aluminum as the main raw material through extrusion and other processing. Aluminum itself has many advantages such as light weight, high strength and corrosion resistance. These characteristics make aluminum profiles widely used in industrial fields, such as aerospace, automobile manufacturing, mechanical equipment, electronic equipment enclosures and other industries.
Second, the feasibility of customization
Flexibility of extrusion process
Extrusion is the key process of aluminum profile production. During the extrusion process, the aluminum billet is passed through a specific mold cavity under strong pressure, thus forming the desired shape. Through the design and manufacture of different molds, a variety of shapes can be extruded, such as round, square, shaped (such as complex grooves, ribs, teeth and other structures) aluminum profiles.
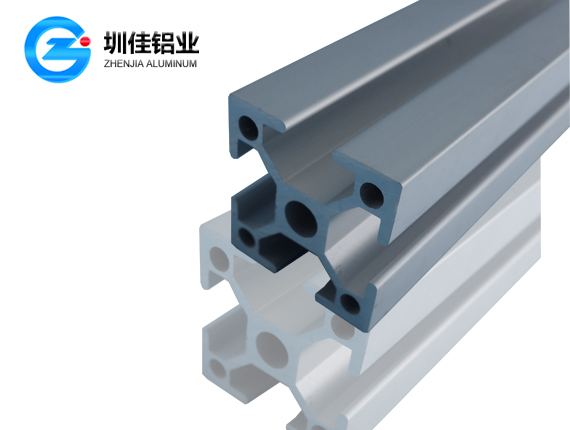
For example, in the construction industry, if aluminum profiles are required for the installation of glass curtain walls, shapes with card slots can be customized to facilitate the installation and fixation of glass. This groove shape can be designed according to specific requirements such as the thickness of the glass and the installation method for extrusion.
Size customization
Industrial aluminum profile
The size customization of aluminum profiles mainly involves the length, width, height and wall thickness of the profiles. In the production process, according to the industrial needs, the size of the aluminum profile can be accurately controlled.
Taking the automobile industry as an example, the luggage rack aluminum profile of the automobile needs to have a certain length and appropriate section size to ensure its carrying capacity and aesthetics. According to the design requirements provided by the automobile manufacturer, the manufacturer can customize the length of the automobile roof length, cross-section shape and size to meet the load and installation requirements of the aluminum profile.
Machining fit
In addition to the extrusion process, the shape and size of the aluminum profile can be further customized through subsequent processing. For example, through mechanical processing (such as milling, drilling, etc.), specific installation holes and connection positions can be machined on the surface of aluminum profiles.
It is assumed that in the frame manufacturing of automation equipment, customized aluminum profiles may require accurate screw holes in specific locations for mounting motors, sensors, and other equipment. At this time, drilling, tapping and other processing can be used to process the aluminum profile after extrusion, so that it meets the assembly requirements of the equipment frame.
Adjustment of material properties
According to industrial needs, the material properties of aluminum profiles can also be adjusted to better meet the requirements of the use after the shape and size customization. For example, by alloying (adding other elements such as magnesium, silicon, etc.), the strength and hardness of aluminum profiles can be improved.
If the customized aluminum profile is used for industrial shelves with large loads, the content of alloying elements can be appropriately increased to ensure that it can be processed into the desired shape and size at the same time, improve its carrying capacity and prevent deformation of the profile.